
Demonstration and learning factories help companies try out new things – under the close eye of industry experts – and put their own technologies, product or customer interfaces to the test before making an investment. Regional ‘Mittelstand 4.0 centres of excellence’ that receive funding from the Federal Ministry for Economic Affairs and Climate Action, and the Centre of Excellence for the ‘Digitalisation of Skilled Crafts’ help German SMEs become more aware of Industrie 4.0, and provide them with information, training and opportunities to test their Industrie 4.0 applications. A map entitled ‘use cases Industrie 4.0’ shows where Industrie 4.0 solutions are already being used in Germany today.

There are more than 200 practical examples that demonstrate that innovative processes for linking plant equipment, IT systems and business models more closely are already being developed and implemented by companies and research institutions. In the two funding programmes entitled ‘Autonomics for Industrie 4.0’ and ‘Smart Service World’, the Ministry for Economic Affairs and Climate Action is already providing close to €100 million to foster research and innovation in the field of Industrie 4.0. Industrie 4.0 is a central focus of the Federal Government’s Digital Agenda. Smart, digital production processes present great opportunities for businesses – particularly for SMEs. The German government wants to utilise the enormous potential of Industrie 4.0 to strengthen Germany’s manufacturing base. Key social and political organisational tasks Only if all the relevant stakeholders from industry, academia, politics and society are heard and if they work together as partners from an early stage onwards can we make the fourth industrial revolution a success. However, such transversal issues cannot be dealt with by one single company or industry. Unified standards, IT security and data protection therefore play a crucial role. However, as industry becomes more digitalised and connected, the number of interfaces and the amount of data that is exchanged will increase.

The digitalisation of industry will not only transform value-creation processes but also give rise to new business models and new prospects for employees. This offers enormous potential for innovation and business in Germany, as some 15 million jobs depend directly and indirectly on the manufacturing industries. Cooperation: working together to harness new opportunities In addition, the automated analysis processes that are used can reveal maintenance needs and production downtime risks. This means capacity can be used in the best way possible. IT support will make it possible to dynamically adapt processing stations to a changing product mix. This will change the demands made of industrial manufacturing. For example, production lines need no longer be limited to a single product. The use of digital technologies in industry will lead to the development of a large number of new production methods, business models and products. Producing in a more flexible, customised and efficient way Across company and industry borders, a wide range of economic stakeholders are also becoming part of this trend: from medium-sized logistics companies to specialised technical service providers and creative start-ups. But it is not only ‘smart factories’ that are becoming increasingly connected. Driverless transport vehicles manage the logistics processes and the flow of materials without any human intervention. Service robots help people do physically demanding work in the assembly shop. In Industrie 4.0 factories, smart machines control production processes by themselves. Financing for start-ups, company growth, and innovations.
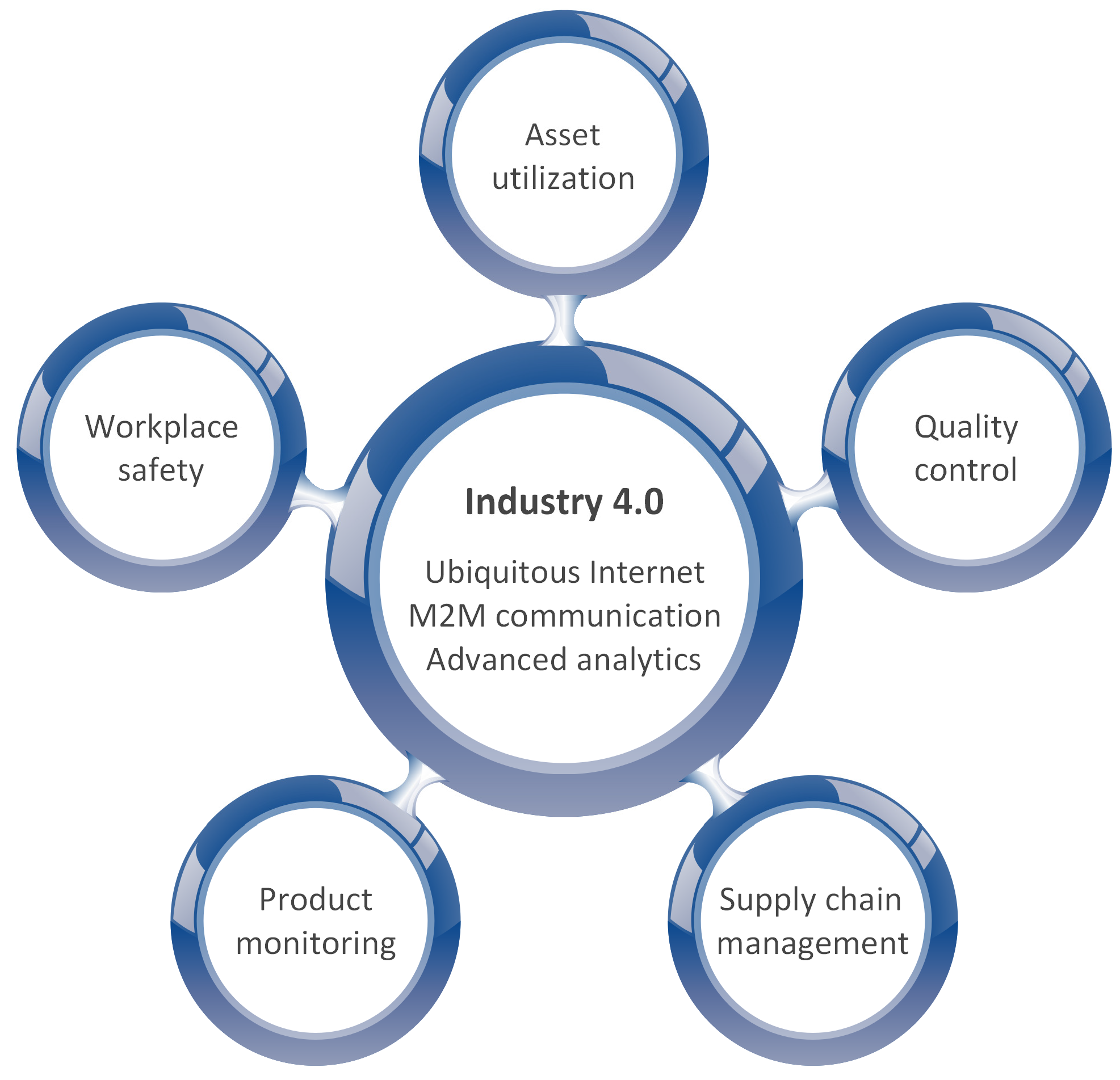
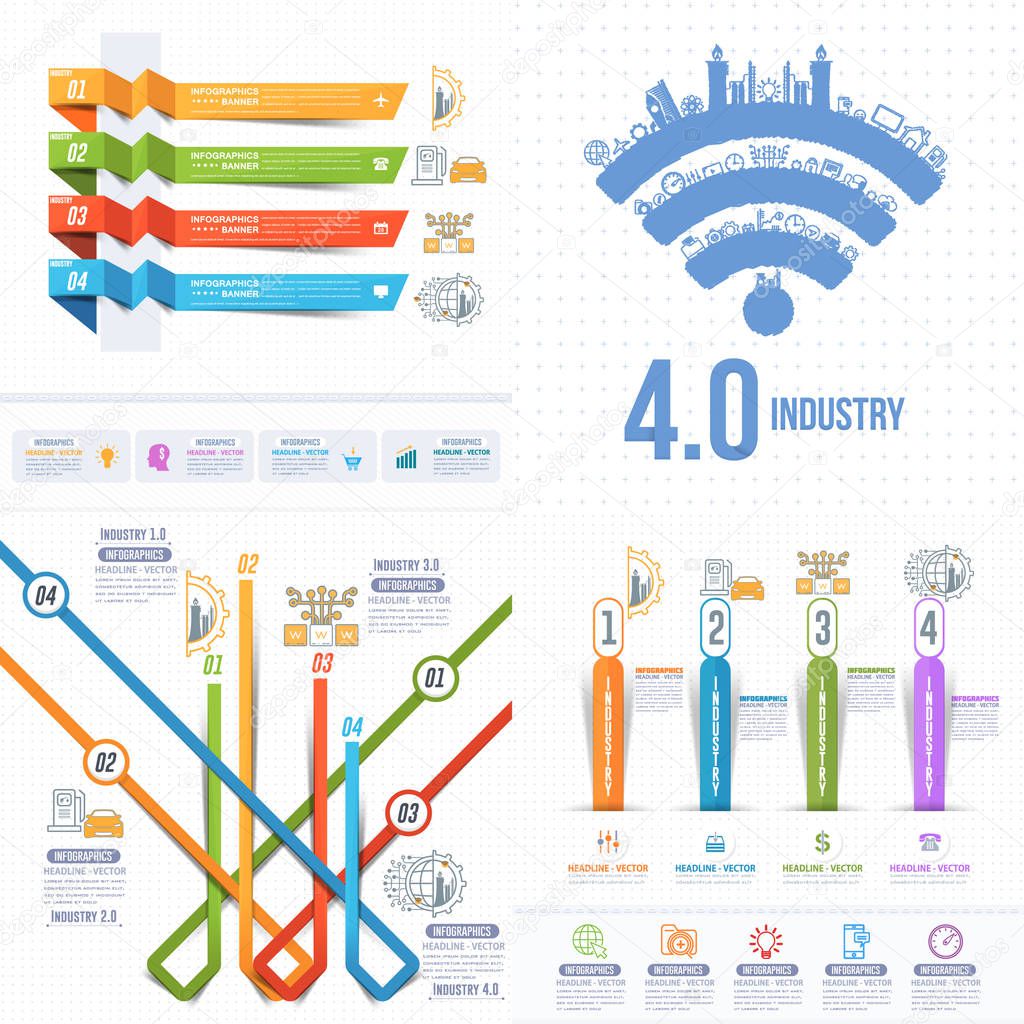
